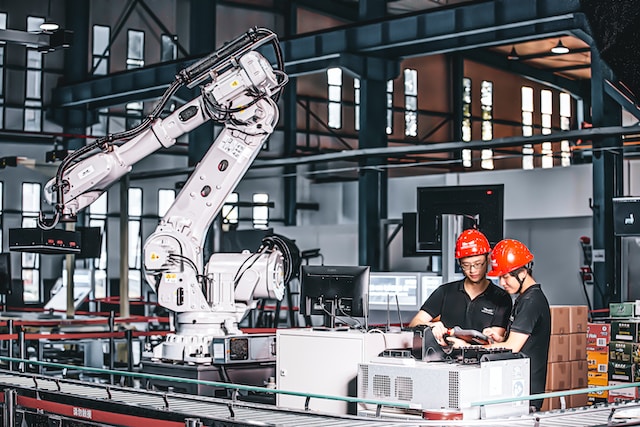
Functions of Injection Mold Builders
Injection mold makers use complex processes to create high-quality injection-molded plastic products. They also offer a variety of secondary services. Injection molding requires high upfront costs and long lead times. It’s easier to make drastic design changes by re-tooling the plastic mold.
Tooling
After the design is finalized and the CAD file is ready for fabrication, engineers convert it into an injection mold using CNC milling machines. It is called tooling or tool building and can be done in either steel or aluminum. High-volume injection molds will typically be constructed in steel due to their durability. For complex designs that have undercuts, engineers may use sliding side-action cores or redesign the part to avoid them. It is preferable to avoid undercuts if possible because they add cost, complexity, and maintenance requirements to the injection molding process. Minimizing the wall thickness of a design can reduce cycle times by 50% to 75%. It can also save costs by avoiding high-grade finishes. For example, embossed text is easier for CNC machines and more economical than engraved or printed text. Also, raising text to an easily read level is an inexpensive and practical way to include logos, warnings, or diagrams.
Designing
A well-designed injection mold handled by injection mold builders ensures the correct amount of molten plastic fills the cavity. It must also allow for easy maintenance and repairs. The injection mold designer will consider the number and type of cavities in part and the size and location of cooling lines. It will also consider the injection molding process, including the parting line, slide mechanism locations, and draft angles. It is essential to avoid undercuts, which increase the cost and time of the injection molding cycle. Instead, designers may add a sliding side-action core or another in-mold mechanism, which should move perpendicularly. It will ensure that the part is not deformed as it slides in and out of the injection mold. In addition, the design should include a boss where fasteners can be attached, or threaded inserts added.
Testing
As with any machine, injection molds require testing to ensure they operate correctly. It includes detecting defects, making adjustments, and monitoring performance over time. The molded plastic’s primary functions include shape and texture. Secondary functions include features like ribs, bosses, snap-fits, and embossed text. Finally, tertiary functions can arise from specific mold components and features. During molding, trapped air can inhibit the flow of melted plastic, which may cause short shots or incomplete parts. Poor design is another common source of short shots, such as abrupt geometry changes or holes. A guided ejector system is essential for the proper ejection of molded plastic. This feature drives ejector pins into seated positions before the mold closes, preventing them from being pulled away by the cores or slid off by a sliding side-action core. A protective sleeve on any slide is also recommended to prevent premature wear of the ejector pins.
Manufacturing
Creating an injection mold requires suitable materials and systems for distribution, cooling, and ejection. The ejector pins in the mold must be appropriately positioned to guarantee that the final item is released to make plastic goods. The number of cavities in a mold directly correlates with initial manufacturing costs, so fewer cavities reduce overall cost. The size, texture, and draft of the cores and cavities are also significant factors in cost. Details that require additional tooling work, such as undercuts or other complex features, increase the cost of the mold. After the mold is built, it must be inspected before production begins. This step, called First Article Inspections (FAI), is essential to mitigate risk and waste by ensuring the injection mold can reliably produce quality parts for its intended application. The inspection process includes visual inspection, testing, and x-ray scanning of the product to verify its strength and functionality. It also includes a quality control plan to verify the injection molding process produces quality parts consistently and within the specified tolerances.

